Aluminium

What is aluminium?
Aluminium is one of the most abundant metals on earth. In fact, it makes up 8% of the total weight of the Earth's crust. That is why it is one of the most widely used industrial metals - even though it was discovered and isolated only 200 years ago.
Aluminium alloys
Pure aluminium is alloyed with small amounts of other metals to cultivate certain properties – e.g. in relation to machining.
These alloys are divided into 8 series according to EN 573-3, and the alloys are named according to the series. As an example, the alloy 6082 belongs to the 6xxx series and 5005 belongs to the 5xxx series.
Aluminium alloy groups
Alloy group |
Alloying elements |
Properties |
Commonly used for: |
1xxx |
Min. 99% aluminium |
+ Good corrosion resistance, good conductivity, ductile - Low strength |
- Aluminium foil - Architectural cladding - Electronics |
2xxx |
Copper |
+ High strength, suitable for machining - Poor corrosion resistance, not suitable for aesthetic anodising |
- Threads and bolts - Aviation - Military vehicles |
3xxx |
Manganese |
+ Very ductile, suitable for anodising, welding and soldering - Low strength |
- Beverage cans - Packaging - A/C systems, heating and cooling equipment |
4xxx |
Silicium |
+ Suitable for welding and soldering - Low ductility, low strength |
- Beverage cans - Packaging - A/C systems, heating and cooling equipment |
5xxx |
Magnesium |
+ Ductile, often good corrosion resistance - Medium strength |
- Facades - Scaffolding - Automotive |
6xxx |
Silicium and magnesium |
+ Good corrosion resistance, suitable for welding and aesthetic anodising - Low ductility |
- Profiles, e.g. for doors, windows and trailers - Offshore |
7xxx |
Zink, secondarily magnesium and copper |
+ High strength, suitable for machining - Risk of corrosion |
- Airplanes - Military and space equipment - Skiing equipment |
8xxx |
This group contains all alloys that do not fit into any other group. For this reason, there are no common characteristics of the 8xxx alloys. |
What is aluminium used for?
Aluminium is widely used in construction and manufacturing, e.g. for windows, cladding and building materials.
The main advantage of aluminium is the light weight combined with strength and the fact that aluminium can be extruded into many different shapes. This makes the material ideal for lightweight but strong constructions.
You will find many facades with aluminium cladding such as composite panels from STACBOND.
For designs where the aluminium will be visible, e.g. facades or electronics, the metal can be anodised or painted in a colour other than the characteristic grey/silver.
This is done, for example, with aluminium-clad composite windows, which combine the corrosion resistance of aluminium on the outside with the attractive appearance of wood inside the house. By painting the aluminium profile and the wood with the same colour, the difference in the materials is concealed.
You can see examples from our customers here.
Is aluminium weldable?
Aluminium is suitable for welding. But to get to the metal, you need to penetrate the oxide layer which has a melting point of 2060 degrees Celsius. There are different methods for this, including TIG and MIG welding.
Because aluminium is a very good heat conductor, the HAZ (Heat Affected Zone) is larger than you might be used to with other materials. This means that the heat quickly spreads from the weld seam into the material.
Learn more about how to weld aluminium here.
Physical properties of aluminium |
|
Density |
2.7 g/cm3 |
Melting point |
660 °C |
Electrical conductivity |
59.5 %IACS |
Thermal conductivity |
215 W/m*K |
Thermal expansion coefficient |
23.5 µm/m*K |
You can see the mechanical properties and the chemical composition of each aluminium alloy here.
Aluminium is a light but strong material. Compared to stainless steel, aluminium can provide the same strength with significantly less weight. Aluminium is characterised by high thermal conductivity and electrical conductivity, and the natural oxide layer acts as a guard against corrosion.
The main advantage of aluminium is that it has similar properties to copper (conductivity) and stainless steel (corrosion resistance), but with a very low weight. Another advantage is that aluminium can be extruded as profiles.
How to calculate thermal expansion
Aluminium will expand and contract depending on the temperature.
In environments with large fluctuations in temperature, such as outdoors in Northern Europe, it is important to take thermal expansion into account.
The expansion is calculated by using the coefficient of thermal expansion (pure aluminium: 23.5 µm/m*K).
Expansion occurs in all directions. This means that you need to calculate the expansion for the height, thickness and width of the material.
Example
- A sheet of alloy 5754 (coefficient of thermal expansion: 23.7 µm/m*K) is mounted on a facade.
- At -20 °C the plate is 1000 mm
- At +30 °C, i.e. 50 degrees warmer, the thermal expansion is:
23.7 µm/(m*K)*1 m*50 K=1185 µm=1.19 mm
The plate is 1001.19 mm at +30 °C.
Consult the data sheets for more data on specific alloys.
What is rolling direction?
The surface of a rolled sheet or plate will have visible texture lines from when the material was rolled to the correct thickness.
Depending on the intended use of the material, it may be necessary to take the rolling direction into account.
If several parts, sheets or plates are mounted close together, make sure that the texture lines run in the same direction on all parts to achieve a uniform look.
When bending, the rolling direction may affect the bending ability of the material.
If you purchase sawn material, you need to specify the rolling direction. This ensures that the finished panel has the right properties for your intended use. In this example, the sheet will have a rolling direction of 300 mm:
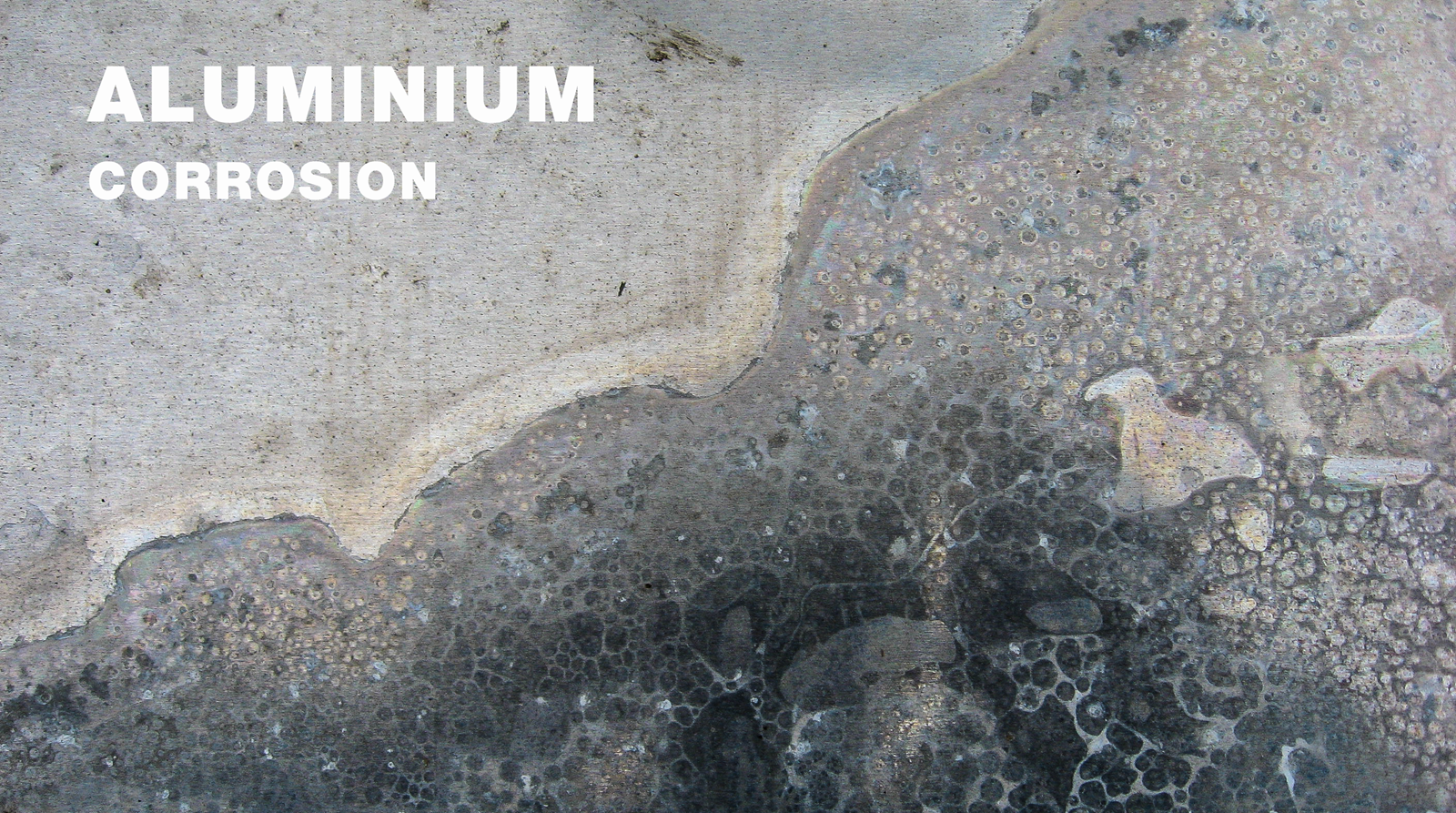
Aluminium corrosion
Aluminium is highly resistant to corrosion in many different environments. This is one of the reasons why aluminium has become so widely used.
But as with any metal, it is important to choose the right alloy for the surrounding environment. You need to know the corrosion class of the specific environment to make the right choice.
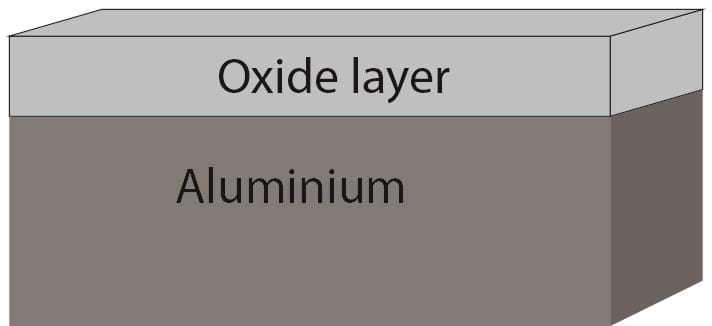
Oxide layer
The secret to aluminium's corrosion resistance is the oxide layer that forms when pure aluminium is exposed to oxygen.
As the oxide layer thickens, it becomes harder for the raw aluminium to react with oxygen, acids, bases, etc. As a result, the metal becomes more and more protected from the surrounding environment.
Anodising is the process of provoking aluminium to form an extra thick oxide layer. The anodising can have a practical or aesthetic purpose.
The optimal pH for the oxide layer is in the range of 4-9. Acids and bases outside this range degrade the oxide layer. This can cause issues if you use the wrong cleaning agent on an aluminium product.
Can aluminium rust?
Aluminium cannot rust – rust only occurs on iron.
But aluminium can corrode if the alloy you choose is not suitable for the environment. As an example, you should not choose a 2xxx alloy for an offshore environment.
Corrosion can also occur if you combine aluminium with another, more noble, metal without a sacrificial anode.
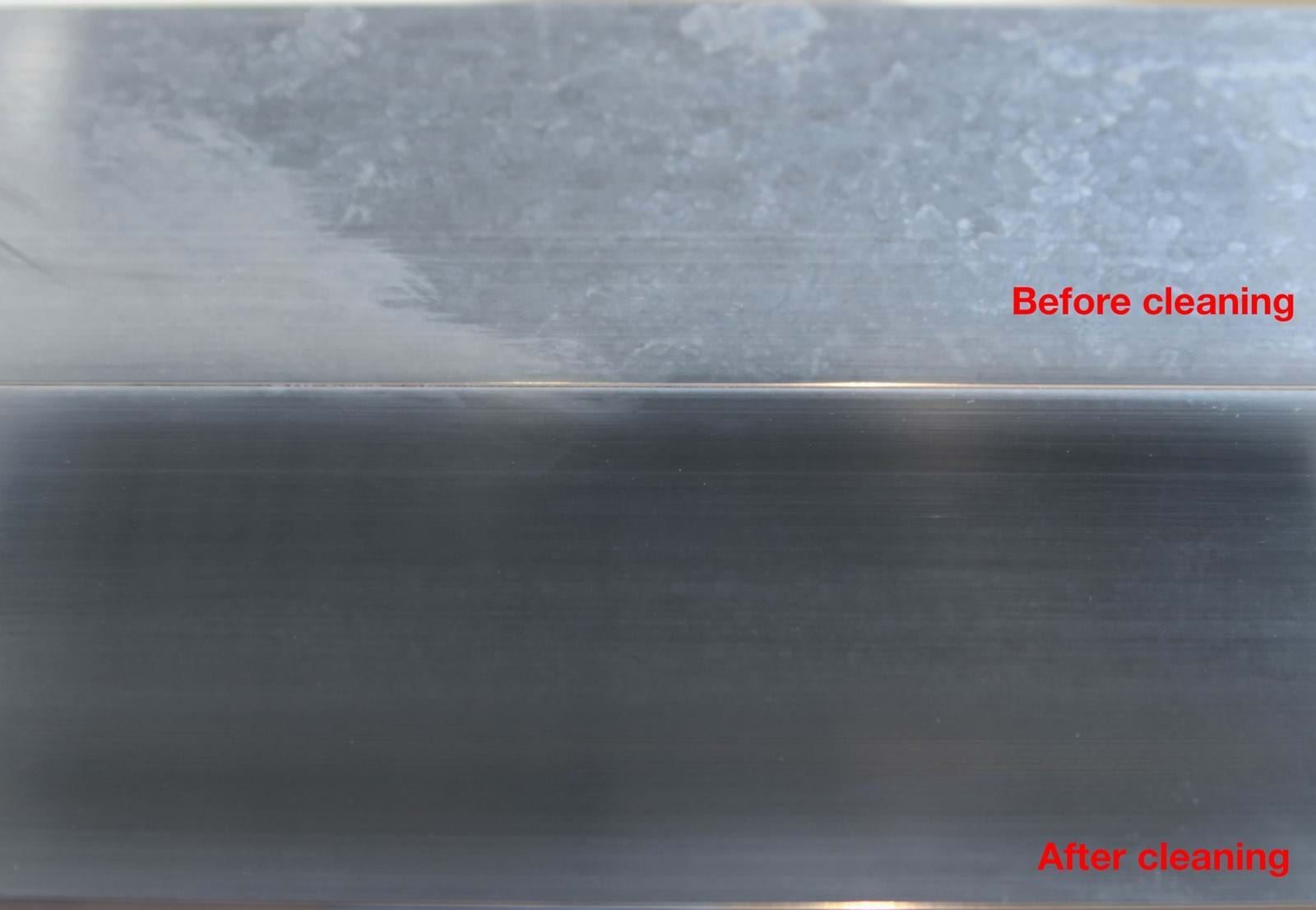
How to clean aluminium
To avoid corrosion and discolouration, it is important to keep aluminium reasonably clean. This is true even if the metal is anodised or painted.
Just like the natural oxide layer, an anodised surface does best with pH values between 4 and 9. Stronger acids and bases break down the layer and provide a good basis for corrosion.
Cleaning agents
The best cleaning agent is clean water, possibly with a soap product with a pH value between 6 and 8. It is important that the cleaning agents do not contain chlorine. After cleaning, rinse the surface with clean water.
Very dirty surfaces can be cleaned with organic solvents such as alcohol, acetone, petrol, thinner, kerosene and turpentine.
Methods for cleaning aluminium
Aluminium is well suited for dry or changeable environments where the material is not wet for long periods of time. Regular rainfall helps keep the surface naturally clean, preventing dirt at moisture building up.
If you need to manually clean aluminium, use this list as a starting point. The list is ranked from the most gentle method (clean water) to the most aggressive (abrasives):
- Clean water
- Mild soap/detergent
- Solvents, e.g. kerosene, turpentine or white spirit
- Non-corrosive chemical cleaners
- Polishing with wax (can cause temporary damage to the oxide layer)
- Sanding with wax (can cause temporary damage to the oxide layer)
- Abrasive cleaner (can cause temporary damage to the oxide layer)